功能安全流程
汽車產業中功能安全開發程序的實施遵循 IATF 16949 和 ISO26262 標準。將功能安全程序納入立錡汽車開發流程中對符合行業標準、確保產品的安全性和可靠性至關重要。透過與汽車產品品質計劃(APQP)、安全計劃、實施安全分析、確認措施和安全案例檔案,我們為專案中的功能安全奠定了堅實的基礎。
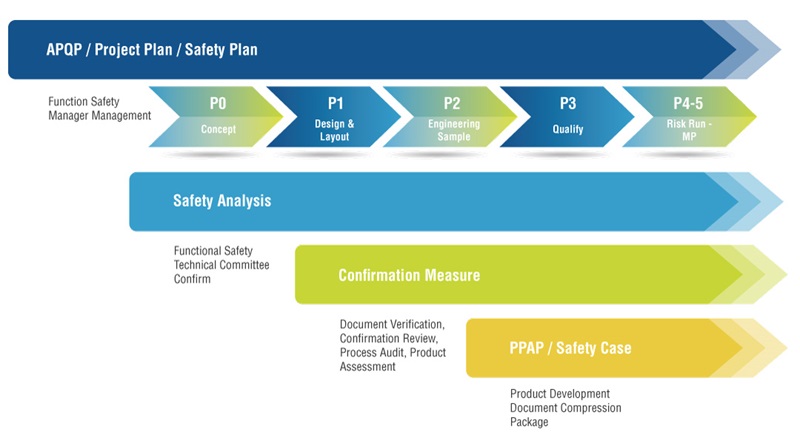
APQP/Project Plan/Safety Plan:
功能安全開發流程的基礎建立在 IATF 16949 和 ISO 26262 標準之上。我們的專案計劃和安全計劃與汽車產品品質計劃(APQP)框架保持一致,這是一個針對汽車產品的全面品質開發計劃。這確保了將安全考慮納入專案的所有階段。
Phase 0 - Concept:
概念階段是對精確性需求最高的階段,因為容易發生人為錯誤。這個階段包括:
- 定義每個參與者的角色。
- 收集來自客戶的安全需求。
- 提出系統的安全概念。
- 審查整個流程和安全計劃,確保組件準備好進行設計。
Phase 1 - Design and Layout:
設計階段用於驗證所有功能方面。主要包括:
- 管理所有與安全案例相關的工作。
- 釋出安全計劃。
- 執行與假定的系統安全概念一致的安全設計。
- 進行失效模式和影響分析(FMEA),以減少 IC 功能和安全機制之間的常見故障。
- 執行定量安全分析(FMEDA),確保 IC 設計滿足功能安全指標(PMHF、SPFM 和 LFM)。
- 確保所有開發工具分類並符合 ISO 26262 標準。
- 如果項目涉及 IP 使用,進行硬體影響分析和風險評估。
- 通過模擬驗證定量安全分析中定義的診斷效果。
- 分析單點故障和常見故障的模擬結果,包括封裝故障分析和定性分析。
- 通過內部獨立團隊管理審核安全案例的流程。
Phase 2 - Engineering Samples:
- 該階段涉及獲取組件的過程。管理外包製造商符合汽車等級要求的合規性。這些訊息由功能安全經理驗證,任何偏差都需要立即審查。
- 對所有安全設計機制及其相關診斷範圍進行品質驗證。
- 通過設計驗證和確認階段完成組件測試和驗證。
- 測試涵蓋 Alpha-site 電氣驗證、AEC-Q100 封裝可靠性認證和自動測試設備(ATE)生產測試。
- 內部獨立團隊對安全案例和流程管理進行確認和審查。
Phase 3 - Quality:
- 所有安全設計機制及其相關診斷範圍均包含在品質驗證範圍內。
- 發布全面的 AEC-Q100 可靠性認證報告。
- 更新安全手冊和安全分析報告。
- 評估功能安全設計是否符合系統設計定義和 ATE 生產測試(CP/FT)。
- 第三方功能安全評估,以確保設計的安全符合產品規劃和假定的系統應用。
- 內部獨立團隊審查安全案例,在獲得批准後完成安全案例。
Phase 4 - Risk Run Production:
- 遵循汽車開發流程標準執行所有監測和評估測試,並評估測試覆蓋率後,產品可以進入量產階段。
- 功能安全經理和指定的協作人確認所有與安全相關的審查,以及所需的評估或測試。
- 在安全案例中記錄所有安全論點,並存檔保存超過 15 年。
- 內部獨立團隊進行功能安全認證,並在完成和發布產品的安全案例之前審查功能安全案例,以使產品進入量產階段。
Phase 5 - Mass Production:
Safety Analysis:
為確保我們的安全措施的堅固性,所有功能安全分析文件都經過獨立單位的嚴格審查流程。這種統一的安全審計包括關鍵分析,如失效模式和影響分析(FMEA)、故障樹分析(FTA)、設計失效分析(DFA)以及失效模式、影響和診斷分析(FMEDA)。
Confirmation Measure:
開發過程的每個階段,從 P0 到 P5,都符合安全措施的要求。所有程序,從需求定義、規範、測試到生產,都經過了徹底的驗證。此外,內部獨立單位已對產品的功能安全設計進行了功能安全審計和評估。
PPAP/Safety Case:
功能安全案例框架建立在 IATF 16949 生產零部件批准流程(PPAP)之上,包括所有安全論點和工作輸出。這些都存儲在配置管理系統的專用功能安全部分。這種方法確保了所有與安全相關的方面都是可追蹤並有檔案記錄的,符合最高的品質和安全標準。